制造业质量管理的数据之困:管理难、应用难、成本高
1. 管理难:数据孤岛与标准缺失的叠加困境
多源异构数据融合难:质量数据涵盖设备传感器时序数据(如振动频率、温度波动)、机器视觉图片(如缺陷特征图像)、工艺参数日志等非结构化数据,不同系统(如MES、QMS、SCADA等)的数据格式与接口标准差异显著。 IT&OT系统孤岛效应:IT系统与OT生产系统分离,数据无法实时互通,生产计划与车间设备脱节,异常数据无法及时反馈管理层,导致质量监控滞后、问题响应延迟,跨部门数据调用耗时长,管理效率低下。 安全合规性挑战:行业合规性(如IATF16949汽车行业质量管理体系 )要求企业数据长期保存以确保可追溯性,但数据孤岛与标准缺失导致数据未合理分层,关键数据检索效率低下,进一步制约质量数据的整合与分析效率,加剧管理难度。
2. 应用难:全链路数据价值的释放瓶颈
分析能力缺乏:数据显示,73%企业缺乏专业数据分析团队,SPC控制图仍依赖人工解读,质量问题重复发生率高,根本原因难以精准定位。工业质检设备产生的海量数据中,仅20%被有效用于模型训练。 智能决策未闭环:AI质检设备普及率提升,但仅有少量企业实现“检测-诊断-工艺调整”自动化链路,大多依靠最终检验发现质量问题,缺乏预测机制,被动应对产品客诉。 知识沉淀不足:质量专家经验未能有效转化为数字资产,核心工艺参数调整逻辑依赖个体经验,知识断层缺乏标准化模型。
3. 成本高:数据治理投入与收益的博弈
存储成本居高不下:机器视觉检测数据呈指数级增长,以国内某头部新能源动力电池企业为例,单个工厂可产生6.46PB/年质量检测数据,法规要求检测数据保存期长达15年,传统NAS存储或机台本地硬盘存储容量不足,需要频繁扩容,且存储硬件采购成本高昂。 AI训练成本陡增:AI模型训练依赖高质量标注数据,企业缺乏统一数据平台面临“标注-训练-迭代”恶性循环,数据重复采集、标注效率低下,标注与训练成本上升。 全链条协同效率低成本高:质量问题解决周期长,未构建统一数据管理平台的企业,跨厂区/产线数据检索调用平均耗时3-4天/次,影响生产效率,徒增管理成本。
AI+数据驱动,解锁制造业质量管理新范式
1. 破局“数据孤岛”:构建全域质量数据资产化
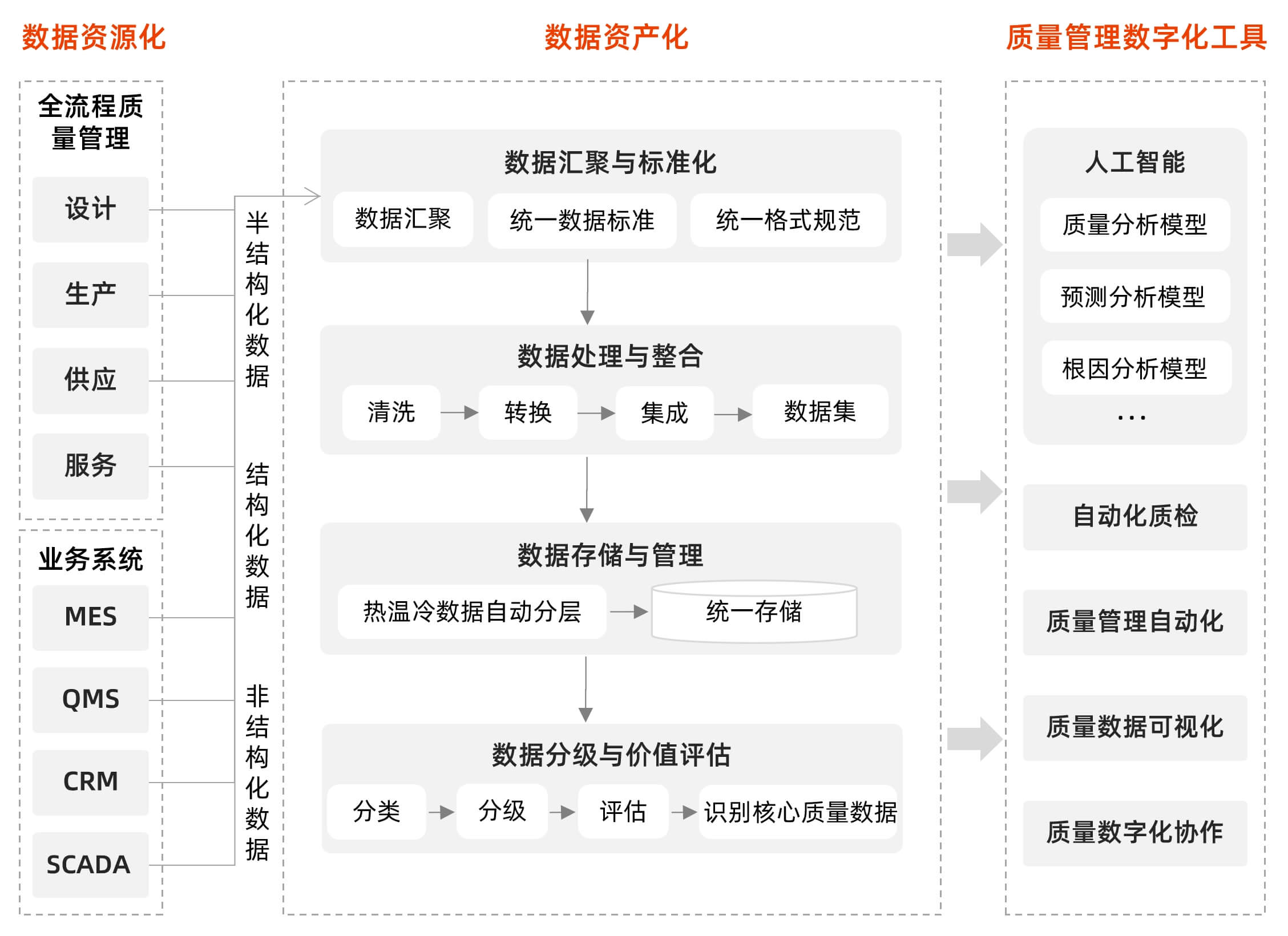
2. 终结“被动响应”:构建数据驱动的主动防御体系
AI为数字化质量管理提供了新的解决思路,其核心是将质量控制从"事后检测"转变为"事前预防",从"经验判断"转变为"数据决策"。通过历史检测数据和机器学习算法,构建质量预测模型,预测可能出现的质量问题和质量趋势,给出工艺参数调整参考,优化质检流程,提高产品良率。
3. 破解“知识流失”:构建质量数据知识引擎
将企业内部的质量知识,包括质量标准、检验规范、故障案例、解决方案等进行全面梳理和整合,形成结构化的知识体系,并通过数据挖掘和自然语言处理技术,从海量的质量数据中提取有价值的知识,并将其存储在知识引擎中。例如,对历史质量问题的处理记录进行分析,总结出常见问题的解决方案和预防措施,供后续参考,形成“数据-知识-决策-反馈”闭环,使企业质量知识资产可沉淀、可迭代、可复用。
4. 降低“质量成本”:数据驱动的精益化变革
基于质量管理与业务价值链深度融合和完善的数据采集,运用大数据和AI技术进行质量数据分析,可以提前识别潜在的质量问题,加强质量策划能力。通过优化生产工艺和流程,提高产品的一致性和可靠性,是降低质量成本的重要途径。此外,针对产线质检数据暴增产生的存储成本高的难题,可以采用智能化的数据管理系统,如杉岩检测数据管理系统IDM,通过AI无损压缩、冷热数据自动分层存储(如冷数据自动归档至磁带库)、到期数据自动清除等数据自动化管理策略,降低存储空间占用,可降低70%数据存储成本。
案例实践:某行业头部动力电池生产企业以数据驱动质量管理变革
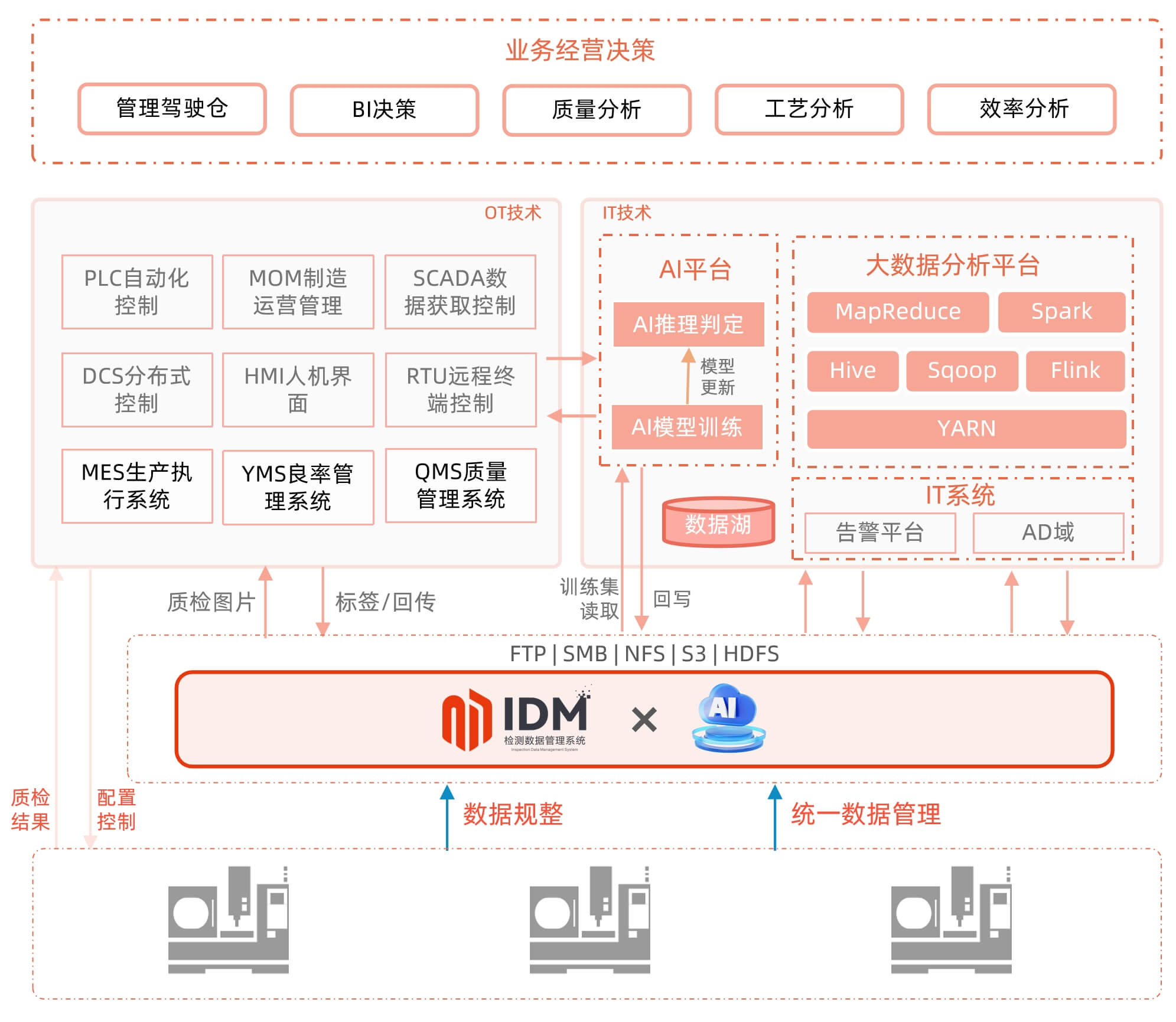
结语:数智融合,智造未来